高真空減壓蒸餾作為一種有效的分離純化技術(shù),在有機化學(xué)、石油化工、生物制藥等多個領(lǐng)域中廣泛應(yīng)用。然而,在實際操作過程中,特別是在處理對熱敏感的目標產(chǎn)物時,如何有效避免其在高溫蒸餾過程中的熱分解風(fēng)險,成為了科研工作者和工程師們關(guān)注的重要課題。本文將探討高真空減壓蒸餾條件下降低目標產(chǎn)物熱分解風(fēng)險的方法。
首先,優(yōu)化蒸餾溫度是關(guān)鍵。在高真空環(huán)境下,物質(zhì)的沸點顯著降低,因此可以通過調(diào)控系統(tǒng)內(nèi)的真空度來適當降低蒸餾溫度,從而減少目標產(chǎn)物因高溫而發(fā)生熱分解的可能性。同時,精確控制升溫速度與恒溫時間,避免溫度驟變導(dǎo)致的局部過熱現(xiàn)象,也是防止熱分解的有效手段。
其次,采用適當?shù)谋Wo劑或穩(wěn)定劑。對于某些易于熱分解的化合物,可以在蒸餾前加入適量的穩(wěn)定劑或者通過共蒸餾的方式引入一種能與其形成穩(wěn)定復(fù)合物的物質(zhì),以降低目標產(chǎn)物在蒸餾過程中的活性,達到抑制熱分解的目的。
再者,改進蒸餾裝置及工藝流程設(shè)計。例如,使用內(nèi)壁涂有惰性材料(如特氟龍)的蒸餾器,可降低目標產(chǎn)物與設(shè)備表面的反應(yīng)活性;采用分段蒸餾或回流冷凝相結(jié)合的技術(shù),既能提高分離效率,又能避免目標產(chǎn)物長時間處于高溫狀態(tài)。
此外,智能監(jiān)控與自動化控制技術(shù)的應(yīng)用也不容忽視。實時監(jiān)測蒸餾過程中的壓力、溫度以及物料變化,并利用先進的PID控制器進行精準調(diào)節(jié),確保整個蒸餾過程始終在安全、穩(wěn)定的范圍內(nèi)運行,有助于較大限度地降低目標產(chǎn)物的熱分解風(fēng)險。
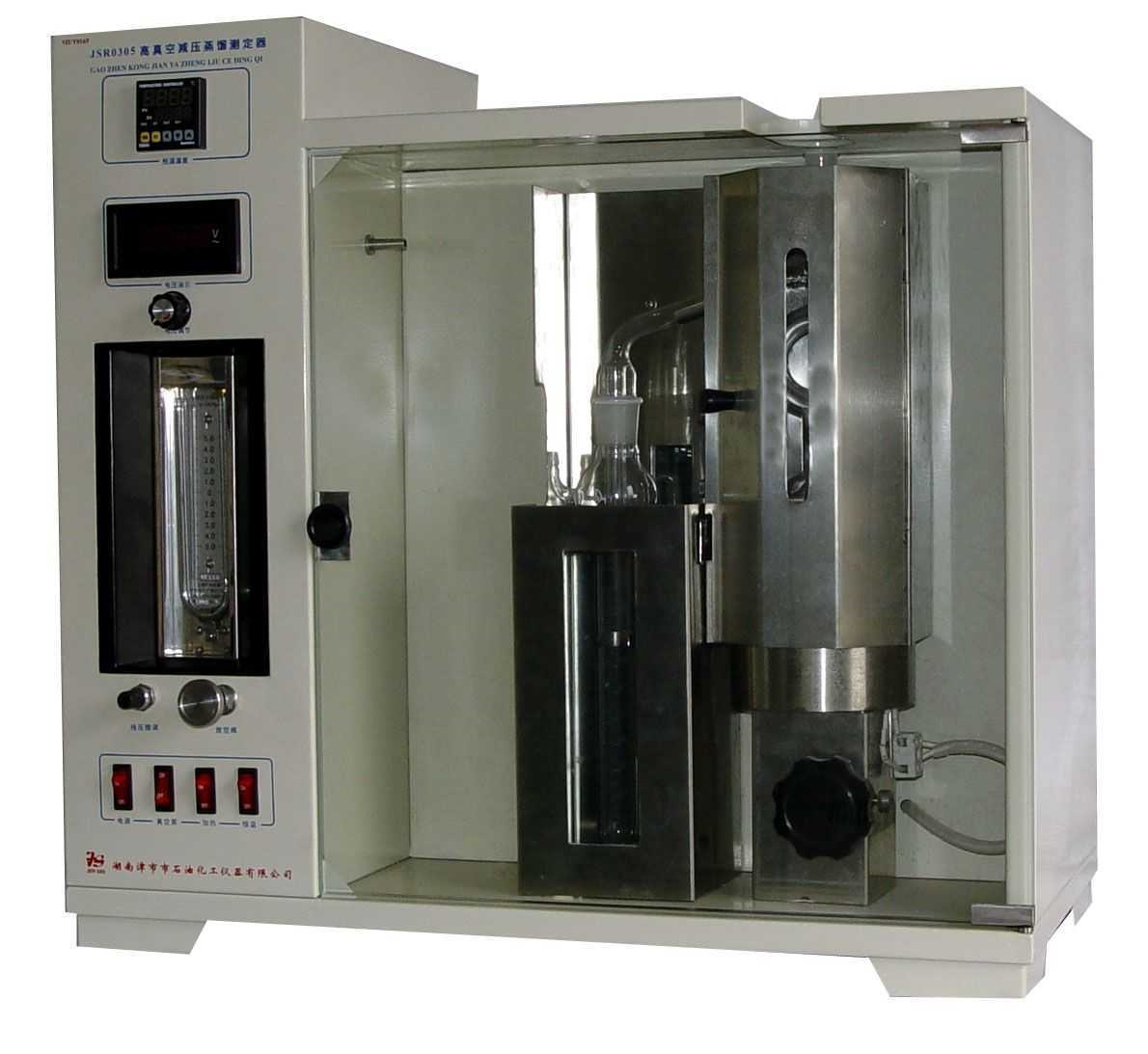
而且,實驗室研究和工業(yè)生產(chǎn)中還需結(jié)合具體目標產(chǎn)物的性質(zhì),不斷摸索并驗證新的保護策略和技術(shù)方法,包括新型冷卻技術(shù)的研發(fā)、微波輔助蒸餾技術(shù)的應(yīng)用等,以期在保證高真空減壓蒸餾效果的同時,有效防范目標產(chǎn)物的熱分解問題,實現(xiàn)更高效、更安全的分離純化過程。